From Layout to End Up: The Full Light Weight Aluminum Spreading Refine Demystified
In the realm of production, the process of aluminum casting stands as a crucial method that has actually fueled markets for years. Each action in this intricate process, from the first layout stage to the last complements, plays an important duty in forming the outcome of the product. What absolutely exists underneath the surface area of this process continues to be a mystery to several. By untangling the intricacies and dropping light on the nuances associated with each phase, a much deeper understanding of the art and scientific research behind light weight aluminum spreading arises. about aluminum casting. Stay tuned as we explore the complete light weight aluminum spreading procedure, uncovering the intricacies that change basic materials right into polished products.
Designing the Casting Mold
When initiating the light weight aluminum spreading process, meticulous interest to designing the spreading mold and mildew is paramount for ensuring the end product's stability and top quality. The spreading mold offers as the foundation for the entire spreading process, dictating the form, measurements, and surface area finish of the eventual aluminum component.
To develop an efficient spreading mold and mildew, designers have to consider various aspects such as the intricacy of the part, the kind of light weight aluminum alloy being made use of, and the wanted homes of the end product. about aluminum casting. Computer-aided design (CAD) software program is usually used to create thorough schematics of the mold, permitting for precise personalization and optimization
In addition, the style of the spreading mold directly influences the performance and cost-effectiveness of the casting procedure. A well-designed mold minimizes product waste, reduces the requirement for considerable post-casting machining, and enhances general manufacturing speed.
Melting and Putting Aluminum
With the design of the spreading mold and mildew completed, the following essential step in the light weight aluminum spreading procedure is the melting and pouring of the aluminum alloy. The procedure begins with packing the light weight aluminum alloy right into a furnace where it is heated to its melting point, generally around 660 ° C(1220 ° F) for light weight aluminum. Crucible heaters, induction furnaces, or gas-fired reverberatory furnaces are commonly utilized for melting light weight aluminum. As soon as the aluminum is molten, it is important to keep the temperature within a particular variety to make sure the top quality of the spreadings.
After the light weight aluminum gets to the wanted uniformity, it is time for putting. The liquified aluminum is very carefully moved from the heating system to the spreading mold. This step requires accuracy and control to prevent problems in the final product. The pouring procedure must be carried out quickly to stop premature solidification and guarantee the aluminum fills the mold and mildew totally. Appropriate pouring methods add substantially to the general quality of the last light weight aluminum casting.
Strengthening and Cooling Process
Upon conclusion of the putting process, the molten aluminum changes into the cooling down and strengthening stage, a crucial phase in the aluminum spreading process that straight influences the end product's honesty and features. As the aluminum starts to cool, its particles arrange themselves right into a strong form, progressively taking on the form of the mold. The rate at which the light weight aluminum cools down is vital, as it influences the material's microstructure and mechanical residential properties. Rapid cooling can cause a finer grain framework, boosting the material's stamina, while slower air conditioning may cause larger grain sizes, influencing the final product's ductility.
During this phase, it is vital to regulate the cooling procedure carefully to avoid defects such as porosity, shrinkage, or internal stress and anxieties. Various air conditioning approaches, such as air cooling, water quenching, or regulated air conditioning chambers, can be utilized based upon the blog specific requirements of the spreading (about aluminum casting). By monitoring and regulating the solidification and cooling down procedure, makers can guarantee the production of top quality light weight aluminum spreadings with the preferred mechanical and metallurgical residential properties
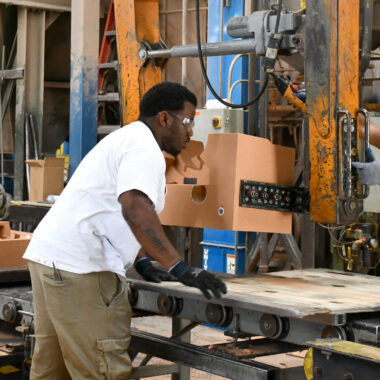
Getting Rid Of the Final Spreading
As soon as the aluminum casting has sufficiently strengthened and cooled down in the mold, the next action in the procedure involves very carefully eliminating the final spreading. This step is vital to make sure that the aluminum component is successfully extracted without any type of damages or flaws.
To get rid of the spreading, the mold and mildew is opened, and the casting is drawn out utilizing different approaches relying on the intricacy of the part and the mold and mildew layout. For less complex shapes, the casting can often be quickly eliminated by hand or with basic devices. For even more detailed layouts, added devices such as ejector pins, air blasts, or hydraulic systems may be needed to assist in the elimination process without causing any harm to the spreading.
After the casting is effectively eliminated from the mold, any excess product such as entrances, runners, or risers that were utilized throughout the casting procedure are cut off. This action helps in accomplishing the final desired form of the light weight aluminum part prior to it goes through any type of additional finishing procedures.
Finishing and High Quality Evaluation
The last in the light weight aluminum spreading process entails careful ending up methods and rigorous top quality assessment procedures to ensure the integrity Get the facts and precision of the cast light weight aluminum parts. Finishing methods such as grinding, sanding, and shot blasting are utilized to remove any kind of excess product, smooth rough surface areas, and improve the aesthetic allure of the final item. These processes not just enhance the look yet likewise ensure that the parts meet the specified dimensional tolerances and surface finish needs.

Conclusion
Finally, the light weight aluminum casting process includes making the mold and mildew, melting and putting aluminum, cooling the casting and strengthening, eliminating the end product, and completed with a high quality assessment. Each step is crucial in guaranteeing the last product fulfills the preferred specifications. By recognizing the entire procedure, manufacturers can generate premium aluminum spreadings efficiently and effectively.
Remain tuned as we dissect the total aluminum casting process, revealing the intricacies that transform raw products into refined items.
With the layout of the casting mold and mildew settled, the next essential action in the aluminum casting procedure is the melting and pouring of the aluminum alloy.Upon conclusion of the putting process, the liquified light weight aluminum transitions right into the strengthening and cooling stage, a vital phase in the light weight aluminum casting procedure that straight influences the final product's stability and features.The last phase in the aluminum spreading procedure includes thorough ending up strategies and rigorous quality assessment methods to ensure the integrity and precision of the cast light weight aluminum components.In conclusion, the aluminum casting process entails designing the mold, melting and pouring aluminum, cooling the casting and solidifying, eliminating the final product, and completing with a top quality examination.